Sweet success for complex machinery lift at sugar factory
Hird has completed a complex contract lift at one of the UK’s largest sugar refineries to replace machinery seven floors up inside a production room.
A 100-tonne mobile crane was used to lift out a conical process vessel while a 60-tonne crane lifted a man basket so a slinger could make adjustments to the lifting tackle during the lift.
The vessel, which weighed 500kg, needed to be replaced as part of planned improvement of the production process at the sugar factory in east London.
Safest, simplest solution
Hird Technical Manager Jason Timmins, the Appointed Person for the contract lifting project, said: “Key to the success of this lift was the smooth and safe transition of the loads out of, and into, the building.
“This required close coordination between our lifting team and our client’s personnel to execute a precise lift plan while maintaining full control of the load at all times.
“The project demonstrated the challenges of factory lifts where machinery can be located in the most hard-to-reach places. It’s up to us to find the safest, simplest and most cost-effective method to lift and move it.”
Hird carried out the machine lift-out on behalf of the factory’s process engineering contractor in a two-step process.
In the first step, a structural load-bearing scaffold frame was installed, creating a hoisting gantry to lift the vessel away from the process plant, move it to the side along a lifting beam, and lower it onto a purpose-made steel stillage (also referred to as a lifting skid).
In the second step, machinery moving skates were used to move the stillage to an opening in the building. The 100-tonne crane was then used to lift the vessel and stillage, weighing a combined 1,500kg, away from the building and down to the ground.
No landing platform
The process was then reversed to lift a new production vessel into place.
The new vessel was placed in the stillage and lifted to the production room opening. The slinger in the man basket adjusted a chain block on one leg of the lifting tackle from the crane to enable the load to pendulum into the building.
This eliminated the need for a scaffold landing platform to be constructed on the outside of the building. During this process a slinger inside the building attached a Tirfor winch cable to the stillage, so it could be pulled into the building and set down in the production room.
The slingers also monitored the lift at all stages, advising the crane operator and lift supervisor via two-way radios.
Hird deployed a five-person lifting team – a supervisor, two slingers and two crane operators – who worked with factory and contractor teams to complete the machinery moving project in five working days.
Extensive enabling alteration
During the lift, the client had to make extensive enabling alterations to the steelwork within the building to accept the new vessel being installed. Hird also assisted its teams with the lifting element of this work.
The 100t mobile crane used was a Terex Demag AC100/4L. It was required to operate with a tip height of a maximum 60m and a maximum radius of 16m, a set-up that had a maximum safe working load of 6,600kg.
The 60t mobile crane that lifted the man basket was a Liebherr LTM1060. It was operated with a maximum tip height of 40m and maximum radius of 11m, a set-up that also provided a SWL of 6,300kg.
Find out more about contract lifting and machinery moving services from Hird. Contact us today. Telephone 01482 227333 or email [email protected].
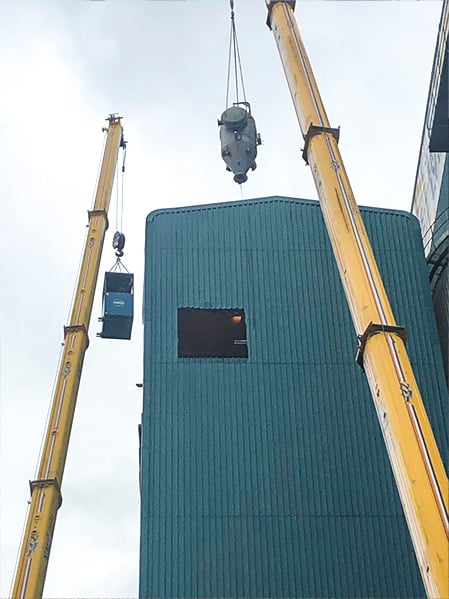
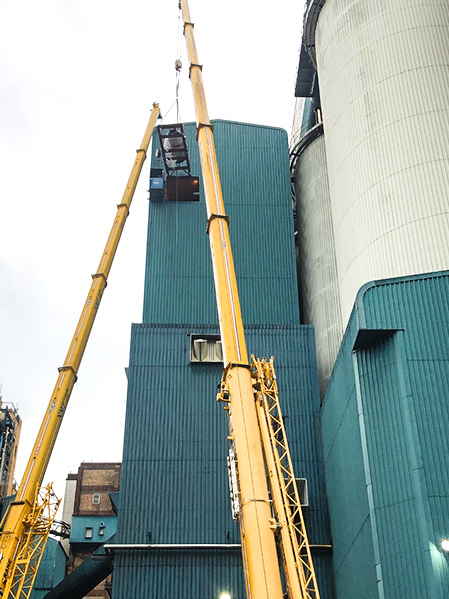
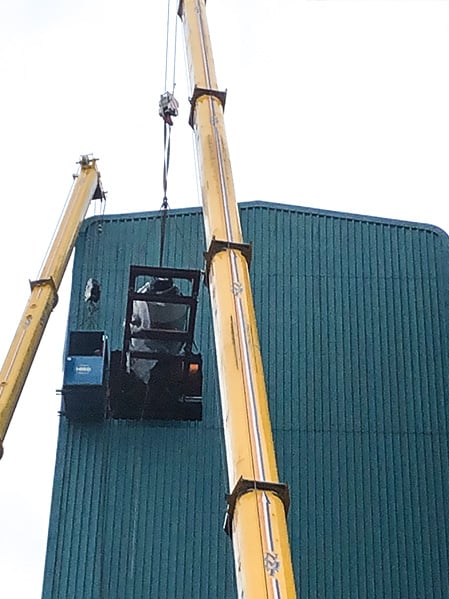